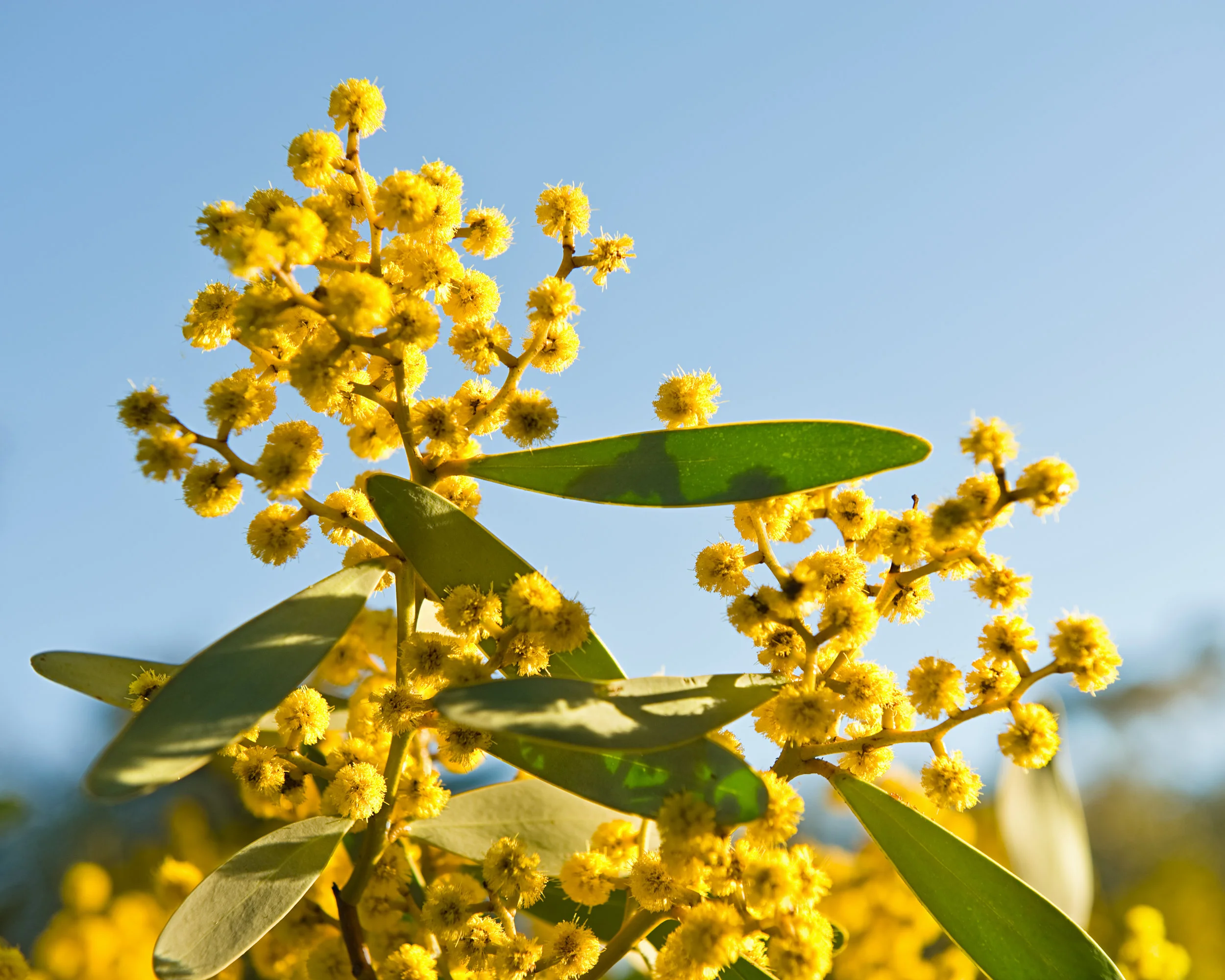
As the Hide and Skin industry becomes increasingly focused on efficiency and quality in the production process, GLP devotes considerable time and effort to ensure it remains a leader in technological developments and environmental sustainability over the long term.
Ongoing investment in the most sophisticated clean processing and tanning techniques allows GLP to optimise production efficiencies within the parameters of a long-term commitment to environmental management and protection. Innovative approaches to effluent treatment and control are given the highest priority to ensure minimal impact upon surrounding environments and ecosystems.
raw materials
All raw materials are sourced and handled in such a way as to minimise their environmental impact.
All AI Topper facilities are committed to the Zero Discharge of Hazardous Chemicals (ZDHC) Joint Roadmap.
External laboratories are used to verify compliance with the globally referenced Manufacturing Restricted Substances List (MRSL). The MRSL is a list of banned chemical substances which are not to be utilised in facilities that process for apparel and footwear for all major international brands. The MRSL establishes acceptable concentration limits for substances in chemical formulations used within the manufacturing process.
innovative solutions
In February 2018, a 500KW solar panel array was installed at GLP, saving over 660 Metric Tonnes of Carbon Dioxide per annum.
Electricity usage at GLP is optimised through the installation of Power Factor Control Units which minimise power generated by suppliers to the site which results in cost savings and reduced energy consumption. Translucent sheeting is also used in processing areas where daylight can be relied on for safe lighting, thereby reducing overall energy consumption.
Environmental sustainability is prioritised across all AI Topper Group sites with a Group Operations Manager charged with implementing initiatives directly linked to the AI Topper Group’s Environmental Sustainability Policy. AI Topper employs a dedicated Environmental Resource at its Wetblue and Brinecuring sites to ensure ongoing environmental innovation, compliance and sustainability initiatives.
Regular management reports are maintained, internal audits are conducted periodically and Annual Returns for Environmental Licenses all validate the achievement of a low impact and sustainable operation over the long-term.
clean production
AI Topper facilities utilise a range of ‘clean processes’ including;
· Green processing and short-term preservation
· Pickle recycling
· Direct Chrome Liquor Recycling (DCLR)
· Chrome recovery
· Hair-saving unhairing technology
· Carbon dioxide deliming
· Beneficial irrigation using tannery effluent
These technologies not only ensure environmental and economic sustainability over the long-term but also establish the AI Topper Group as global leaders in various clean leather production processes with a record of low water consumption and a clean, low-salt effluent discharge.
pollution monitoring data
As required by the POEO Act, Gunnedah Leather Processors makes any pollution monitoring data obtained in compliance with our monitoring conditions attached to our environment protection licence publicly available in a timely manner.
For the most current liquid data please click here
For the most current groundwater data please click here
For the most current soil data please click here
For our Pollution Incident Response Management Plan (PIRMP) please click here
trusted partnerships

Australia has very strict Environmental Protection Laws. AI Topper has a strong partnerships with Regional, State and Federal Environmental Protection Agencies to commit to reducing pollution and waste in order to mitigate adverse impacts and where possible, improve the surrounding environment of processing facilities Australia-wide.
GLP is a participant in the NSW Energy Saver Program, inclusive of Energy Audits conducted by external third parties.
GLP was a recent recipient of a Federal Clean Technology Grant in 2014 and the introduction of induction lighting, a highly efficient process gas vaporization system and a forklift fleet energy-management system were implemented. Total energy savings were approx. 15% at this site alone.
leather working group
As part of its work with leading global brands, Gunnedah Leather Processors has been audited by the Leather Working Group (LWG) for seven audit periods. With a strong environmental focus and clearly set benchmarks across input factors such as a water use, emissions, unit chemical utilisation and hide traceability, The Gunnedah Leather Processors facility has achieved the highest audit level of GOLD for five consecutive audit periods.
“Gunnedah Leather Processors (GLP) process fresh, well fleshed, full thickness, unsalted cattle hides to wet blue. The tannery has adopted a range of clean processes including green processing, hair-saving unhairing, CO2 deliming, direct chrome liquor recycling plus excess chrome precipitation and re-use. All the effluent is beneficially irrigated on land.” Dr Catherine Money, LWG Auditor